Lean è la filosofia di gestione della produzione che si concentra sull’eliminazione degli sprechi e sull’ottimizzazione dei processi per migliorare l’efficienza e la qualità applicabile in molteplici contesti.
La Lean Production, un approccio rivoluzionario alla gestione della produzione, è stata concepita inizialmente da Taiichi Ohno e dal sistema Toyota negli anni ’50 e ’60. Questa metodologia si basa sulla massimizzazione del valore per il cliente minimizzando allo stesso tempo gli sprechi. Attraverso l’eliminazione di processi non necessari e l’ottimizzazione dell’efficienza, la Lean Production si propone di creare un sistema di produzione più snello, flessibile e reattivo.
Ma la Lean va ben oltre la produzione in fabbrica. Questo approccio si è diffuso in molteplici settori, dalla sanità all’ingegneria del software, trasformando il modo in cui le organizzazioni pensano al valore e alla gestione delle risorse. Attraverso principi quali il miglioramento continuo e il coinvolgimento attivo di tutti i membri del team, la Lean Production promuove una cultura di efficienza e innovazione.
L’adozione dell’approccio Lean può non solo ottimizzare i processi produttivi, ma anche migliorare la gestione e l’efficienza in ogni aspetto del business.
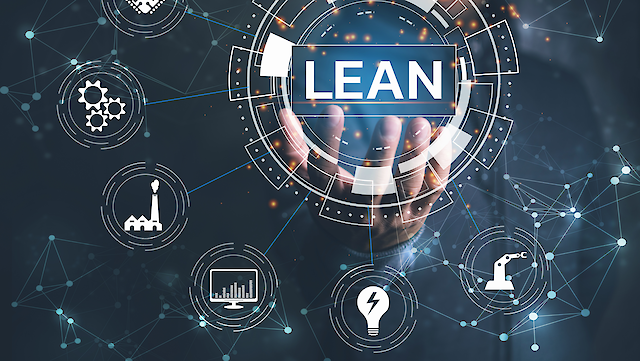
Nel contesto aziendale contemporaneo, c’è una crescente necessità di gestire in modo più efficiente i processi, i team di lavoro e i progetti. Spesso, è fondamentale ottimizzare le fasi di progettazione, produzione e fornitura di servizi per garantire velocità, semplificazione ed efficienza.
Le filosofie Lean e Agile sono spesso menzionate insieme, ma rappresentano due approcci concettuali distinti che si traducono in metodologie di gestione sempre più diffuse nel project management. Questi due approcci condividono molte caratteristiche ma presentano anche alcune differenze.
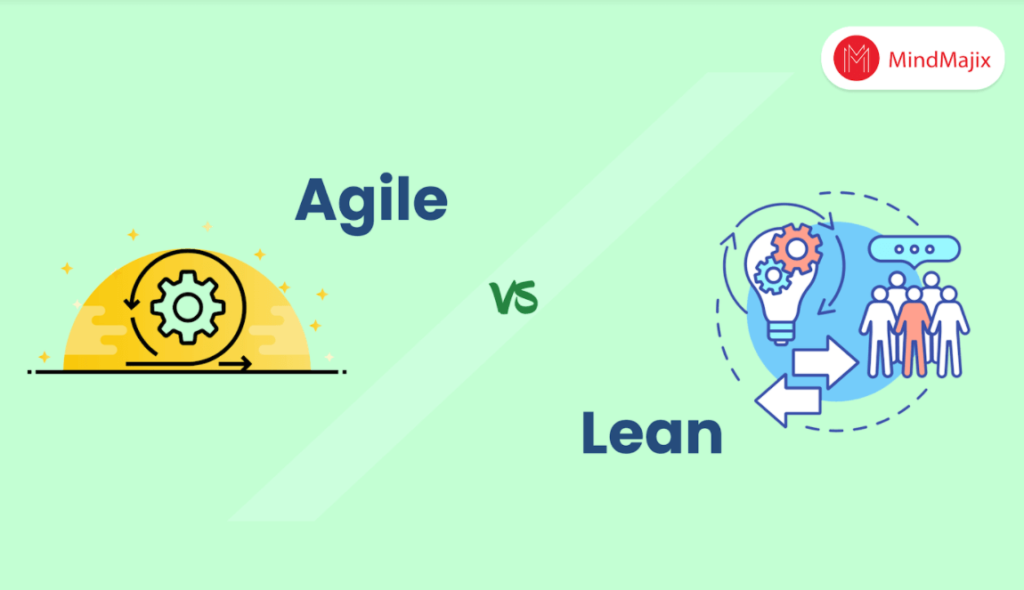
Il concetto principale di Lean Management è quello di “gestione snella” di un processo, con l’obiettivo di massimizzare il valore fornito al cliente riducendo al minimo gli sprechi. In altre parole, si cerca di creare più valore per il cliente utilizzando meno risorse in termini di tempo, materiali e costi. Inizialmente, il Lean è stato sviluppato come un approccio alla produzione, ma ora viene applicato con successo sia nel settore manifatturiero che in quello dei servizi.
Alcuni esperti americani, tra cui W. Edwards Deming, hanno contribuito alla ricostruzione delle capacità produttive giapponesi e hanno introdotto il concetto di “Just in Time” (JIT), un metodo per ottimizzare la produzione riducendo al minimo i materiali in magazzino. Questo approccio non si limita alla produzione ma può essere applicato in qualsiasi contesto in cui i fornitori consegnano materiali in base alla domanda del cliente. L’ingegnere Taiichi Ohno, associato alla Toyota, è considerato uno dei pionieri del Lean Management, che è stato poi implementato nel Toyota Production System (TPS) con l’obiettivo di migliorare la produttività, contenere i costi e gestire le scorte in base alla domanda dei clienti.
I benefici diretti dell’applicazione del Lean Management includono la riduzione dei tempi di consegna attraverso l’eliminazione di attività superflue, nonché la riduzione dei costi operativi. Questo approccio mira a eliminare sprechi come scorte e risorse umane non necessarie per aumentare l’efficienza e ridurre i costi. La riduzione degli sprechi porta a una migliore qualità dei prodotti e dei servizi, il che si traduce in un miglior servizio per il cliente. La filosofia Lean è centrata sul cliente e mira a migliorare la qualità del prodotto finale, garantendo al consumatore un servizio di assistenza migliore e processi di supporto più efficaci. Inoltre, il coinvolgimento delle persone nel processo di miglioramento, promosso dai leader del pensiero snello, contribuisce a migliorare la soddisfazione e la fedeltà dei dipendenti, creando un ambiente di lavoro più sicuro e riducendo i rischi.
Un aspetto chiave è il concetto di “pull“, fondamentale nel sistema Lean, e si riferisce a una filosofia di produzione e gestione che si basa sulla creazione di flussi di lavoro altamente efficienti e sulla minimizzazione degli sprechi. La filosofia “pull” è spesso contrapposta al concetto di “push”, che è più comune nei sistemi di produzione tradizionali.
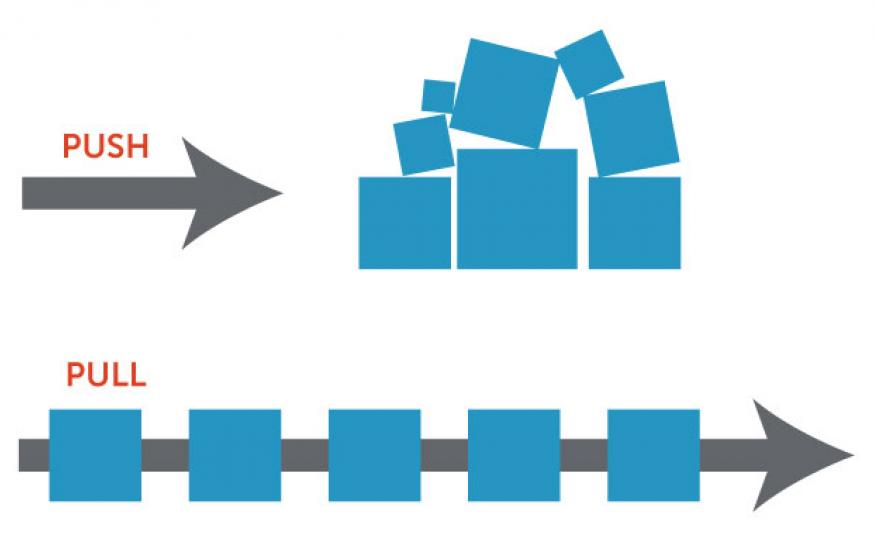
Nel contesto del Lean, il “pull” si riferisce all’idea di creare prodotti o fornire servizi solo quando c’è una reale richiesta da parte del cliente o dell’utente finale. Questo significa che la produzione o la fornitura di servizi viene attivata solo quando un cliente effettua un ordine o quando si verifica una richiesta effettiva, piuttosto che produrre in eccesso basandosi su previsioni o pianificazioni anticipate. In altre parole, il sistema “pull” è guidato dalla domanda del cliente anziché dalla produzione di massa.
Ecco alcuni aspetti chiave del concetto di “pull” nel Lean system:
- Flusso continuo: Il sistema “pull” mira a creare un flusso di lavoro continuo e senza interruzioni, in modo che i materiali o i servizi si muovano attraverso il processo di produzione o erogazione solo quando necessario. Ciò riduce al minimo gli inventari inutili e gli sprechi legati all’accumulo di materiali o prodotti non richiesti.
- Produzione su ordine: I prodotti vengono realizzati solo quando un cliente effettua un ordine specifico. Questo consente di evitare la sovrapproduzione e di rispondere alle esigenze dei clienti in modo più rapido ed efficiente.
- Gestione delle scorte: Nel sistema “pull”, le scorte vengono ridotte al minimo necessario per garantire la produzione continua. Ciò riduce i costi legati all’immagazzinamento e al mantenimento delle scorte.
- Riduzione degli sprechi: Il concetto di “pull” contribuisce a identificare e ridurre gli sprechi all’interno del processo produttivo, poiché si evitano produzioni in eccesso, attese e movimenti non necessari.
- Focus sulla qualità: Poiché il sistema “pull” si basa sulla produzione solo quando c’è una reale richiesta, c’è un maggiore controllo sulla qualità del prodotto o del servizio, poiché ogni elemento può essere attentamente monitorato e controllato.
In sintesi, il concetto di “pull” nel Lean system promuove la flessibilità, l’efficienza e la risposta rapida alle esigenze dei clienti, mentre riduce al minimo gli sprechi e gli inventari inutili. Questa filosofia è ampiamente utilizzata nelle industrie manifatturiere e nei settori dei servizi per migliorare la gestione dei processi e l’ottimizzazione delle risorse.